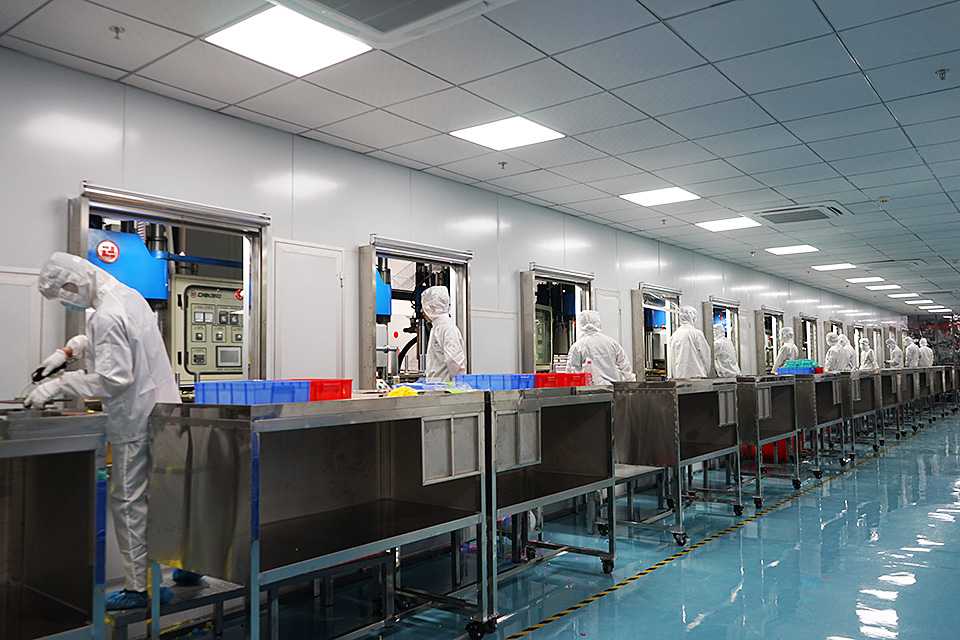
Silicone Compression Molding
A cost-effective molding method for producing high-quality silicone products
Compression molding is one of the most basic and cost-effective processing methods of silicone rubber molding. Also, it is one of the lowest cost molding methods compared with other methods such as injection molding. It is widely used in silicone rubber and plastic industries.
What is Silicone Compression Molding
Silicone compression molding is a manufacturing process used to create high-precision silicone rubber components. This process involves the use of a preheated mold cavity, where uncured silicone material is placed and then compressed under high pressure. The combination of heat and pressure causes the silicone to flow and conform to the mold's shape, curing it into a solid state. This method is often used for rapid prototyping and producing high-quality silicone rubber products. Whether for medical devices, automotive components, or kitchenware widget, baby set, pet accessories, houseware products, offers high-strength and durability.
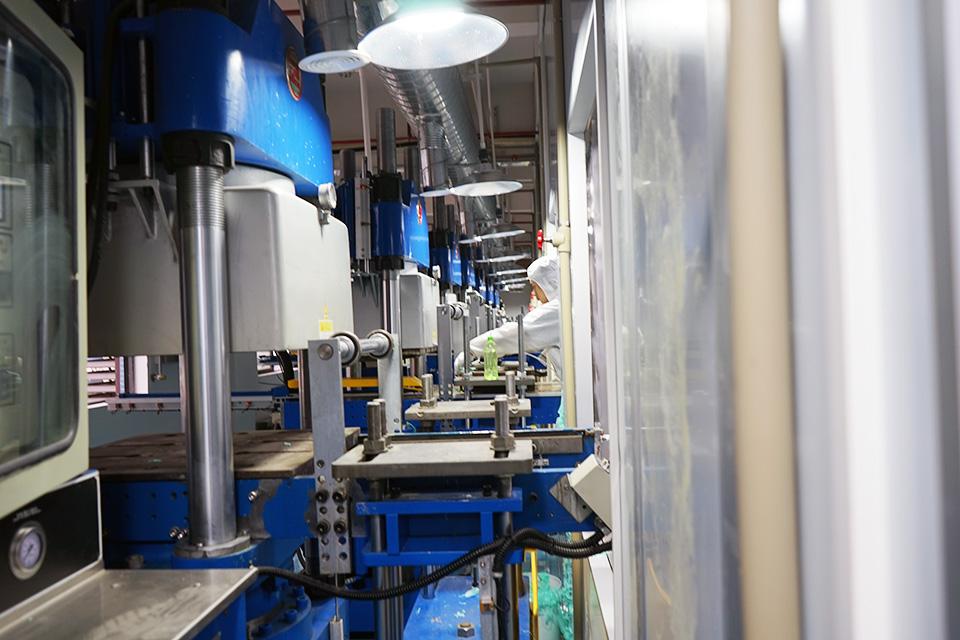
Process of Silicone Compression Molding
1. Mold Design and Creating
Mold Design:A metal mold, typically made from steel or aluminum, is designed based on the desired shape and specifications of the final product. You can send your 3D files of the product to us, our expert engineer can design the mold for you.
Mold Creating:After finalizing the design, creating a metal mold involves several precise steps. First, CNC milling machines carve out the mold's cavities and cores from steel or aluminum, following the 3D CAD model. For finer details, Electrical Discharge Machining (EDM) is used. Once the machining is done, the cavities are polished to achieve a smooth finish, and any necessary textures are added through etching or laser engraving.
At Bogue Silicone, we have our own molding department to ensure every step meets our high standards for quality and precision.
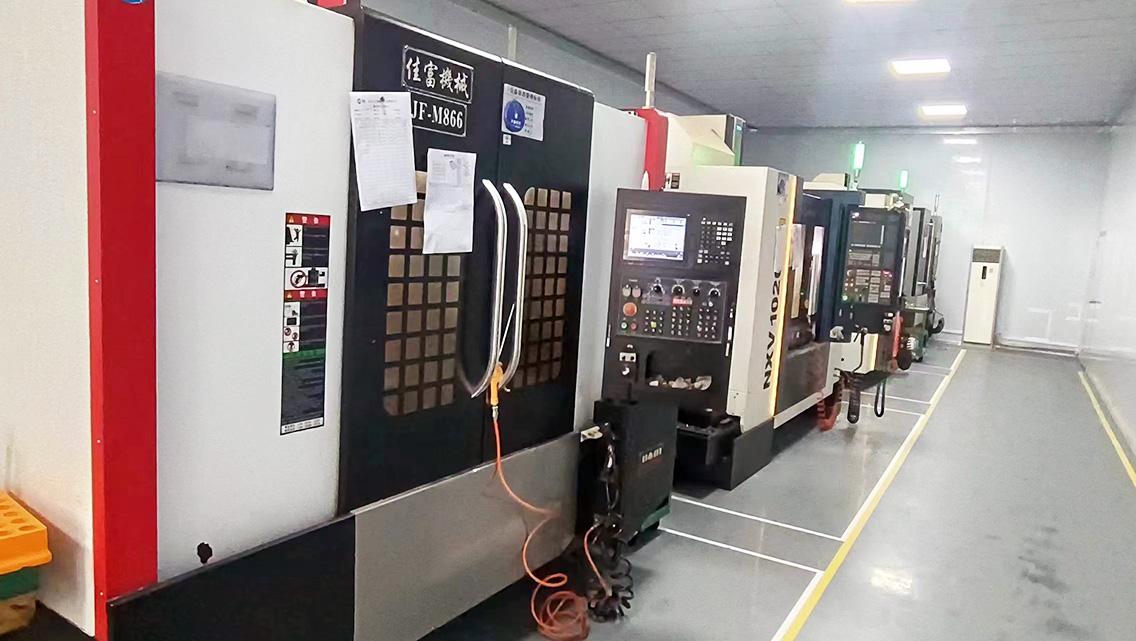
2. Material Preparation
Before the compression molding process, we would prepare the silicone raw materials. The material is selected based on the requirements of the final product such as hardness, heat resistance and other properties.
The selected silicone raw materials will be mixed in a two mill roll machine, in this process, we will add pigment to adjust the color of the silicone rubber material, add curing agent and other additives to adjust the property of the silicone raw material.
After mixing, operators cut the silicone rubber material into slices of various lengths and widths based on the product's weight and shape.
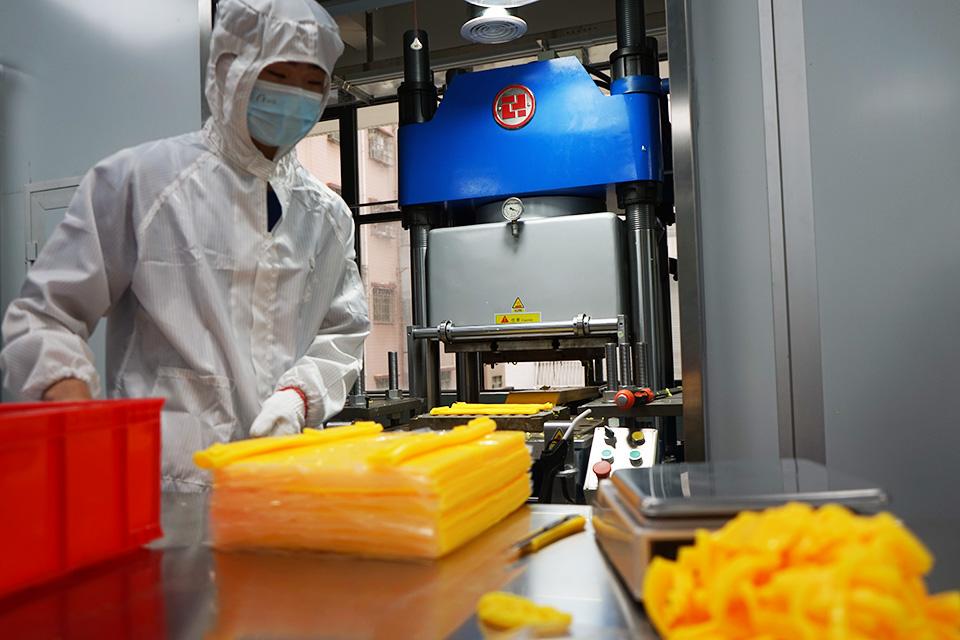
3. Placing the Silicone
The operator clean the metal mold cavity and place the silicone rubber material slice in the every open cavity of the metal mold.
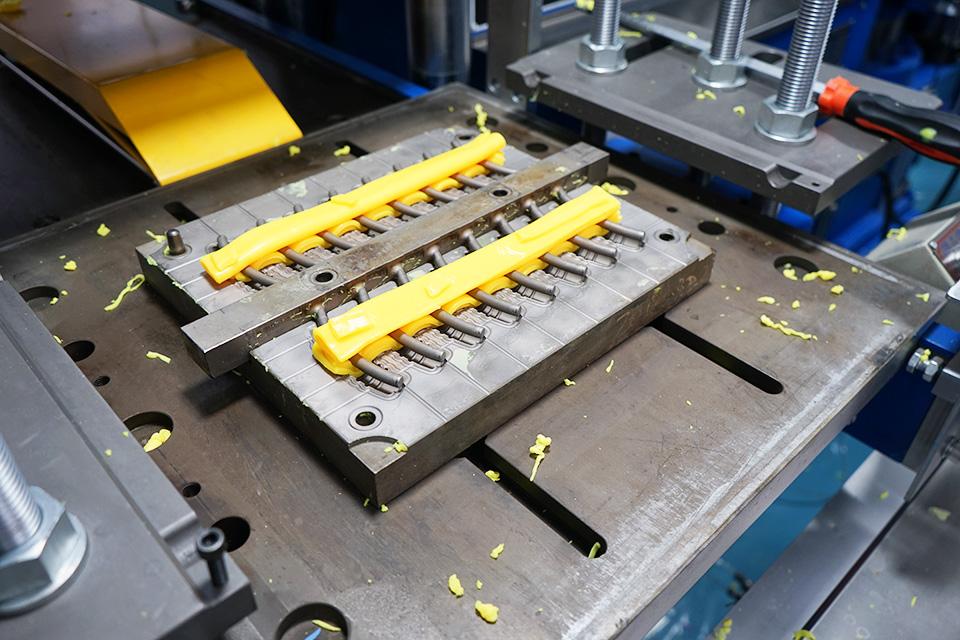
4. Molding
Compression: The mold is closed, and pressure is applied to compress the silicone. This pressure causes the silicone to flow and fill the mold cavity completely, taking the shape of the mold. Curing: Heat is applied to the mold, causing the silicone to cure (vulcanize) and solidify into its final shape. Compression molding machines keep the temperature and pressure to cure the material into the shape wanted.
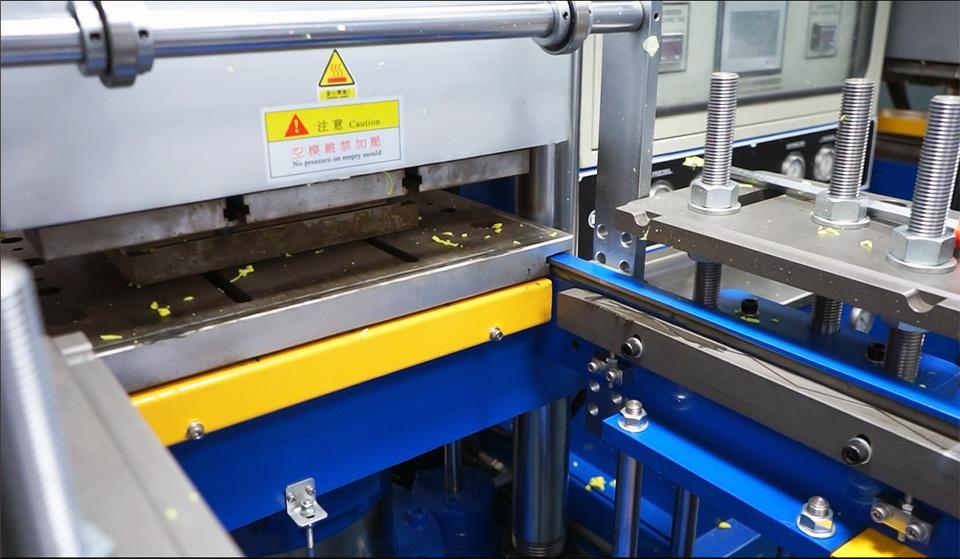
5. Demolding
Part Removal: Once the silicone is fully cured, the mold is opened, and the molded part is removed. This may require additional trimming or finishing to remove any excess material or flash.
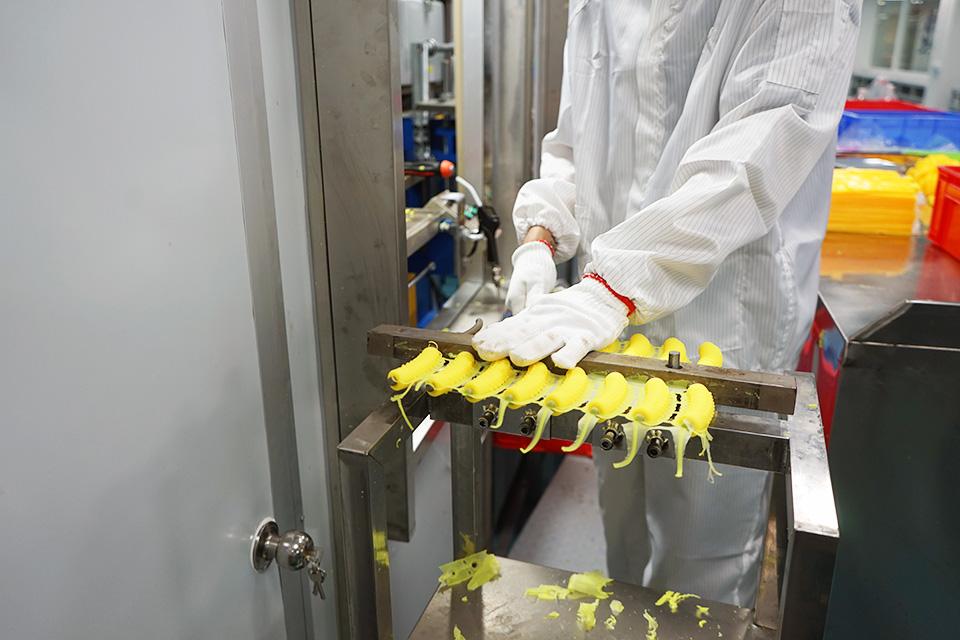
Benefits of Silicone Compression Molding
The molding technique offers several advantages that make it a preferred method for producing high-quality silicone parts and products. Here are some of the key benefits:
- Precision and Consistency: Compression molding ensures that each part produced meets exact specifications, which is crucial for applications requiring high precision. The process provides consistent quality across all produced parts, reducing the risk of defects and variations.
- Cost-Effective: Compared to other molding processes, silicone rubber compression molding often has lower tooling costs, making it an economical choice for both low and high-volume production. The process is well-suited for producing large quantities of parts with minimal material waste, further reducing costs.
- Versatility: Silicone compression molding can create parts of varying sizes and complexities, from simple gaskets to intricate medical devices. The silicone material can be tailored to meet specific requirements, such as hardness, color, and temperature resistance, making it suitable for diverse applications.
- Durability and Longevity: Silicone parts produced through compression molding are durable and long-lasting, reducing the need for frequent replacements. Silicone is resistant to ultraviolet (UV) light and ozone, preventing degradation over time and ensuring longevity.
- Design Flexibility: The molding process allows for the creation of complex shapes and detailed features that may be challenging to achieve with other manufacturing methods. Multiple parts can be produced simultaneously using multi-cavity molds, increasing production efficiency and reducing cycle times.
- Rapid Prototyping: The process supports rapid prototyping, allowing for quick design iterations and faster time-to-market for new products. Advanced curing techniques can speed up the production process, resulting in shorter lead times.
Applications of Silicone Compression Molding
As the most common and cost effective technique, it is used across various industries to produce a wide array of products, including:
- Baby: Bibs, placemats, bowls and other feeding set, teethers, bottle nipples and toys.
- Kitchen: Silicone cupcake molds, ice cube trays and other utensils.
- Houseware: Silicone cups, bags and other tools.
- Pet: Pet feeding bowls, mats and fun toys.
- Medical: Syringe stoppers, seals, gaskets, and other medical-grade components.
- Automotive: Engine gaskets, vibration dampers, and other automotive parts.
- Electronics: Keypads, seals, phone cases, earphone cases and other electronic components.
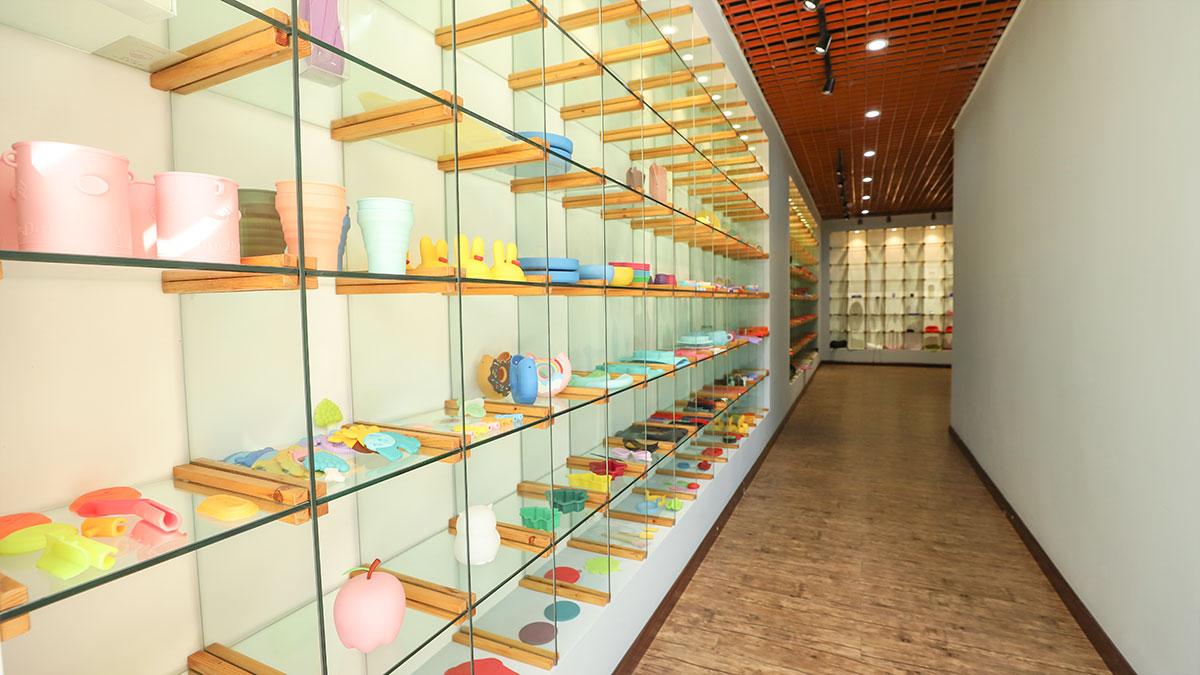
Why Choose Silicone Compression Molding
Because it is an excellent choice for manufacturing high-quality silicone parts due to its precision, cost-effectiveness, and versatility. Whether for medical devices, automotive components, or consumer products, this process offers unparalleled performance and reliability.
By understanding the process and benefits of silicone compression molding, businesses can make informed decisions about incorporating this technique into their manufacturing operations. If you're considering silicone compression molding for your next project, welcome to contact us.
Frequently asked questions
If you have anything else you want to ask, reach out to us.
Start Your Project Today
Transform your ideas into reality with our expert solution and advanced facilities for custom silicone products.